【中國耐火材料網】
長期以來,受“有風就有鐵”高強度冶煉思想的影響,一些高爐工藝配套不合理,導致送風系統和煤氣處理系統能力富余太多,浪費嚴重;一些高爐結構設計不合理,導致壽命短,噸鐵折舊費用高;一些高爐指標欠佳,能耗過高,導致噸鐵成本過高;一些高爐工藝選擇不當,導致生產維護成本高;一些高爐建設時技術不成熟,導致環保不達標。以上種種缺陷,帶來很大的成本壓力和環境壓力,嚴重影響到鋼企的市場競爭力。
針對以上問題,從設計技術的角度出發,可以通過挖掘原配套系統的潛力,采用合理爐型、可靠薄壁本體結構、高效節能冷卻系統、高風溫頂燃式熱風爐、環保底濾水渣工藝及環保節能物料轉運等技術,實現高爐煉鐵的升級改造,確保高爐的高效、低耗、長壽和環保,達到降本增效、提升市場競爭力的目的。
優化爐型,提升高爐生產指標
長期以來,一些高爐因利用系數高就被認為效率高、技術水平高,從而得到眾多鋼鐵企業的青睞。但實際上利用系數過高的高爐(尤其是部分中小高爐)普遍能耗高、噸鐵成本較高。尤其是在目前的微利時代,這些高爐的缺陷逐漸凸顯出來,甚至被貼上落后產能的標簽。
優化爐型,選擇合適的單位爐缸面積工作爐容(Vw/A)。高爐的生產指標不僅與原燃料條件和操作制度息息相關,而且與高爐爐型有密切的關系。為什么一些高爐尤其是中小高爐容易強化冶煉、產量高,但能耗較高,其根本原因在于單位爐缸面積對應的工作爐容偏小。
爐缸面積越大,燃燒燃料越多,煤氣量就越大,產量也會相應增加。但是單位爐缸面積對應的工作爐容(Vw/A)與煤氣在爐內的停留時間是密切相關的,它直接影響到煤氣利用率。據統計,經濟技術指標較好的高爐空塔爐缸煤氣流速或者爐腹煤氣指數ν為58m/min~66m/min,工作容積內煤氣平均壓力也相對穩定。要保持煤氣在爐內足夠的停留時間,必須有合理的Vw/A范圍。由于中小高爐工作容積內煤氣平均壓力較小,Vw/A應該更大,而不是現在中小高爐比大高爐小得多的狀態。當然煤氣停留時間也不宜過長,在爐內6s~7s時,煤氣基本完成了自身熱能與化學能的傳導,因此需要一個合理經濟的Vw/A。
爐型優化改造投資并不高,并可適當挖掘原工藝潛力。高爐工藝流程中,高爐本體所占總投資的比例并不高,大約10%左右,高爐其他約90%的投資都是與產量掛鉤的,跟高爐本體大一點、小一點關系不大。假設高爐不以提高產量為目的,僅為了改善生產指標,適當增加工作爐容100m3,其投資并不是增加3000萬元(假定按照30萬元/立方米爐容計算),而是只增加300萬元或者更低,因為爐缸的投資大于爐腹及以上部位。如果將厚壁高爐改造成薄壁高爐,工作容積增加,投資反而下降。
如果適當增加爐容,降低冶煉強度和利用系數,提高煤氣利用率,那么假設燃料比降低10kg/t,1000m3級高爐每年就節省近1000萬元,僅半年就可以收回增加工作爐容的投資,今后每年增加1000萬元的利潤。
淘汰部分落后高爐,適當增加改造高爐的容積,尤其是適當擴大工作容積,選擇合適的Vw/A,保證適宜的煤氣流速和足夠的爐內停留時間,提高煤氣利用率,噸鐵耗風量及煤氣產生量都會相應減少。同時,挖掘送風和煤氣處理系統的潛力,可以提高高爐產量,降低燃料比,降低噸鐵成本,真正達到高產低耗,實現提升競爭力的改造目的。
采用先進可靠技術,延長高爐壽命
目前,我國高爐平均壽命與國際先進水平相比,有5年~10年的差距,究其原因,設計、操作、維護等方面均存在一些問題。近年來,煉鐵技術飛速發展,如果不運用這些技術成果,仍然采用已經落后淘汰的技術對高爐進行原樣大修,結果就會導致生產指標不能改善,噸鐵成本仍然居高不下,損失巨大。
高爐長壽的關鍵在爐缸,爐缸的可靠性決定了一代爐役的長壽。爐缸壽命主要取決于爐墻結構是否合理、冷卻能力是否足夠及冷卻能力是否得到充分的發揮等。
合理的薄壁爐襯結構。高爐改造,可以采用薄壁爐襯結構,適當增加爐腰直徑,縮小爐腹角和爐身角,調整合適的Vw/A。采用密排水管的球墨鑄鐵冷卻壁、鋼冷卻壁,甚至銅冷卻壁,并滿鑲磚,以確保爐腹及以上爐墻的壽命。薄壁高爐并不是為了節省耐材、降低投資,而是將厚壁高爐經火法修正后,指標較好時期的內型在一代爐齡中固定下來,使得高爐在整個一代爐齡中都能保持高效低耗狀態運行。要強調的是,薄壁高爐不能沿用厚壁高爐內型簡單地將冷卻壁熱面推移到厚壁內型線位置的做法。那樣既不能獲得較好的生產指標,又會導致冷卻壁過早破損,致使高爐短壽。
合理的爐缸結構。這主要包括以下6個方面的內容:一是采用斜爐缸結構,二是穩定且密封的陶瓷杯結構,三是提升碳磚及搗打料質量,四是適宜的風口、鐵口設計,五是健全的監測系統,六是合理的烘爐制度。
高效節能的冷卻系統。同種材質和工藝的冷卻壁,管壁溫度和熱面溫度都可以看作一定熱流強度條件下冷卻壁的冷卻能力。溫度越低,冷卻壁冷卻能力越強。冷卻能力與管徑、水量、水速以及比表面積,可以通過對3種型式爐缸鑄鐵冷卻壁的對比看出其關系,如表1和圖1。由表1和圖1可以看出,采用小管徑密排設計的冷卻壁換熱能力比大管徑的要好,而不是水管越大、水量越大,冷卻能力就越強。小而密的冷卻水管布置的優點在于:可以提高冷卻能力;降低冷卻壁熱面溫度和對爐墻冷卻的不均勻性,降低自身熱應力,延長使用壽命;減少供水量,降低運行成本;減薄冷卻壁,降低投資。
爐腹至爐身下部區域,可采用組合式冷卻壁。其近年來在一些高爐上已得到成功應用,即在鑄鐵冷卻壁熱面部分燕尾槽內插裝銅冷卻條,提高鑄鐵冷卻壁的冷卻強度。銅冷卻條作為渣皮“錨固釘”,使得冷卻壁熱面容易形成更加穩固的渣皮保護層。組合式冷卻壁既具有易結渣皮壽命長的優點,又克服了銅冷卻壁冷卻過度造成渣皮太厚,繼而頻繁脫落給高爐帶來的操作問題,同時投資較銅冷卻壁大大降低。
高效的傳熱體系。盡管爐缸采用合理的結構、高強度的冷卻系統,但如果爐墻有間隙,傳熱系統遭到破壞,耐材不能得到有效的冷卻,爐缸安全仍然面臨嚴重威脅。
由于耐材和爐殼膨脹很難同步,如果冷卻壁和碳磚之間搗打料沒有搗實,或者搗打料和碳磚有質量問題,冷卻壁和耐材之間出現氣隙就在所難免。在氣隙存在的情況下,傳熱體系一旦遭到破壞,耐材就不能得到有效的冷卻。要想解決這個問題,須要從冷卻壁的安裝結構入手。
按照常規設計,冷卻壁是固定在爐殼上的,爐殼膨脹和冷卻壁完全同步。而現在很多工程采用“無間隙冷卻結構”專利技術,將冷卻壁掛在爐殼上,設置排斥設施(如彈簧),通過排斥設施的反力,將冷卻壁推向耐材,保證冷卻壁在任何時候都與耐材緊密接觸,充分發揮其冷卻作用。“無間隙冷卻結構”技術安裝冷卻壁時,將冷卻壁固定在爐殼上,待碳磚砌筑,寬縫搗料后,適當松開螺母,再焊接封罩,可將冷卻壁固定銷、灌漿孔和“無間隙冷卻結構”統一在一套設備中。
應用節能環保技術,提升競爭力
通過高爐改造,采用高溫節能的旋切式頂燃式熱風爐、環保底濾爐渣處理工藝、環保節能的卸料車和轉載技術等高效、節能、環保技術,可以實現高爐煉鐵節能減排、改善環境、提升競爭力的目標。
超高風溫熱風爐技術。提高高爐鼓風溫度,不僅可以降低高爐冶煉的燃料消耗,而且有利于增加噴煤量,降低焦比,對于降低噸鐵能耗和生產成本的效果是明顯的。近年來,很多高爐入爐風溫雖然有所提高,但與先進高爐1250℃左右的風溫相比還是有差距的。
在高爐升級改造中,提高風溫一般可以采取以下措施:一是將內燃式熱風爐改造為旋切式頂燃式熱風爐。二是提高廢氣溫度,既能提高熱風爐蓄熱量,強化換熱,又能提高煤氣、空氣預熱后溫度,也不增加運行成本,是提高送風溫度的最佳措施。改善爐箅子的材質,優化支撐結構,使得爐箅子和支柱能夠承受450℃甚至500℃以上的廢氣溫度。三是改進混風方式,將混風管接至助燃空氣支管,從燃燒器助燃空氣噴口進入熱風爐,根據熱風出口溫度的變化調節混風量。四是改進熱風管系結構,采用低應力熱風管系。
環保底濾技術。環保底濾高爐爐渣處理技術是一種經濟、環保、省地的新型爐渣處理新工藝。環保底濾工藝技術有以下特點:一是蒸汽集中排放,無熱水池,及時抽干過濾池,實現無水過濾,爐前和過濾區域無蒸汽,環境好。二是過濾池應用滲透過濾工藝,渣水分離徹底,過濾后渣中含水量低于0.12t/t渣,同時,渣池具有暫時儲存功能。三是冷水沖渣,抓渣時過濾池內無沖渣水,顯著減少蒸汽排放。四是過濾后的循環水中懸浮物含量低于30mg/m3,系統管道、閥門、水泵等幾乎無磨損,過濾系統無運轉設備,安全性和作業率高。清水泵電能消耗低,節能效果明顯。五是過濾池過濾,抓渣采用橋式抓斗起重機,設備少,故障率低,作業安全、可靠。六是通過提高過濾速度,過濾池面積較常規底濾工藝減少一半;總的占地面積和冷水INBA(因巴法)相當,約650㎡(不含皮帶)。七是一次性投資及運營成本低。環保底濾與轉鼓法工藝的比較見表2。
環保礦焦槽技術。礦焦槽系統產生的大量粉塵,對環境及工人健康造成嚴重危害,因此,建議在礦焦槽系統設計中,采用環保卸料車。此外新型高效、節能、環保的原料運輸及轉載系統,可降低礦焦槽系統除塵能耗,減少環境污染。
現階段開發的環保卸料車將卸料管和除塵管道分開,減小了除塵通風的阻力,氣流順暢,同時避免了皮帶頭輪空隙的漏風,最大程度地改善了除塵效果。
新型高效、節能、環保的物料運輸及轉載系統通過軟件模擬設計出控流曲線溜槽,降低了料流速度,減少了成品物料的破損量,減少了粉塵量并減弱了粉塵氣流。在除塵密封方面,該系統通過在皮帶機頭部采用升降式靜電吸塵擋簾,采用高效的新型雙層密封自降塵導料槽,以及在導料槽系統上增加粉塵阻尼減壓器等措施,降低導料槽落料點的風能,降低氣壓,降低風速,進一步自降塵和降低除塵風量。礦焦槽系統槽下皮帶數量多,每條皮帶的下料點多且相對集中。新型轉載系統適合于幾個下料點集中除塵,除塵風量相應降低,環保效果明顯改善,運行成本大幅度下降。
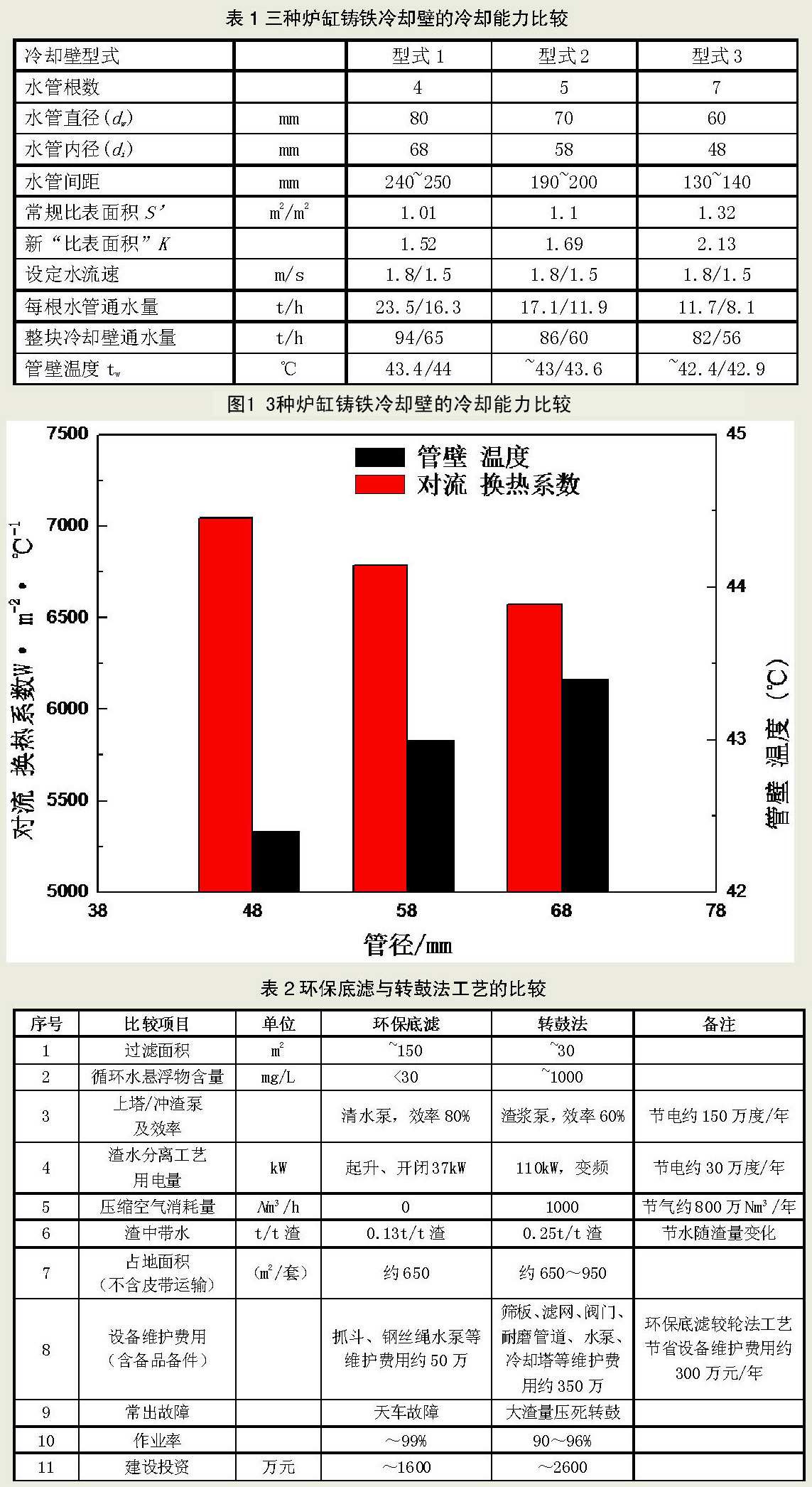
(來源:中國冶金報)